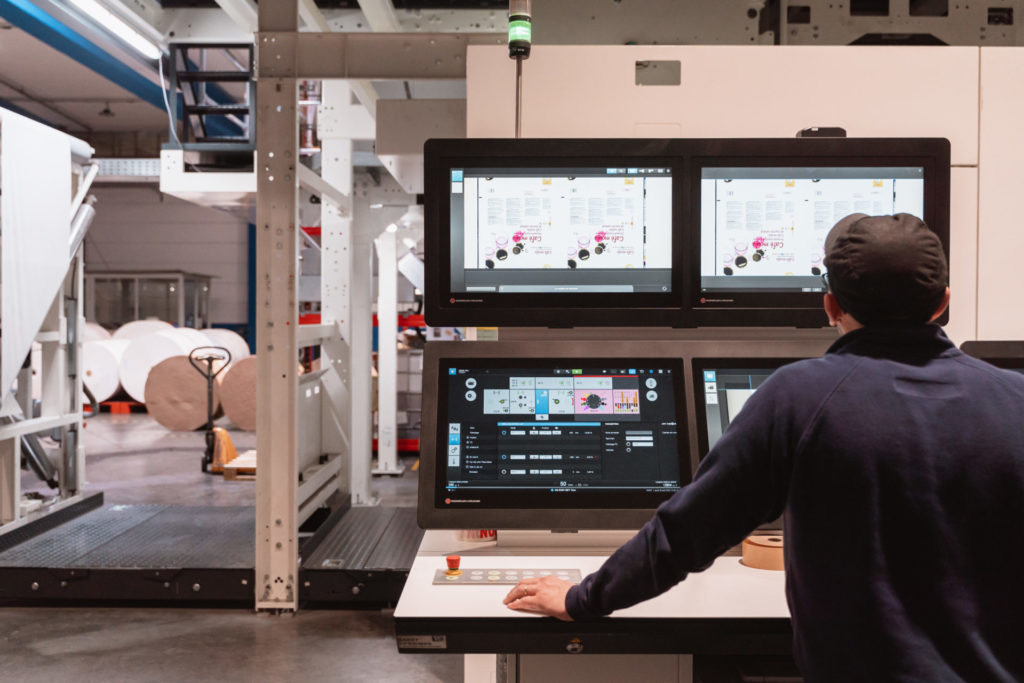
Since the 16th century, the field of printing has continuously evolved. From the first ever printed book to paper packaging through flexographic printing, let’s explore the evolution of these techniques together.
We all know the story of the man with the long beard working in his workshop in Mainz, Germany. That’s the story of Gutenberg and his remarkable advancement for humanity.
Thanks to his invention, it became possible to reproduce books at a “high speed” for the time. Certainly much faster than a reclusive monk scribing away in his monastery.
Although it took a long time for books to become widespread, it was nonetheless a revolution!
Of course, when we hear “printing,” we automatically think of books or literature. But have you ever considered the diversification of printing since then?
Semoulin Packaging takes you on a tour of its facilities to introduce you to a striking printing technique: flexography.
From the birth of printing to flexography
It was in the 15th century that Johannes Gutenberg created the first mechanical press with movable type. His goal? To reproduce texts in quantity for sharing! He became the first to print the most widely circulated book in the world at the time, the Bible.
While the primary aim was to disseminate writings, over the centuries, numerous printing techniques have emerged, such as typography or lithography, each advancement offering new possibilities to printers and publishers.
From Gutenberg to Semoulin Packaging, is it just a step?
It might not be obvious at first glance for newcomers, but yes!
By working with paper as professionals at Semoulin Packaging do with flexography, meters (or even kilometers) of paper reels are printed every day in their workshops.
Since its establishment in 1910, the paper packaging company has evolved to equip itself with the best tools on the market and offer unparalleled printing results.
It was in the 1960s that the company acquired its very first flexographic printer before more recently investing in new products that are as impressive as they are efficient.
What is flexographic printing?
Mathieu, the production manager, is the one who introduces us to this piece of engineering directly in the factory. Put on your hairnet and white coat, the tour begins!
Developed in 1952, this technique gets its name from the Greek words “flexos” and “graphein,” which respectively mean “flexible” and “writing.”
“It could be compared to a giant ink stamp,” explains Mathieu, “the product design, the logo, the choice of colors, and everything else is created before being transferred onto the plate.“
The plate, called a cliché, is made of photopolymer material that is flexible and pre-engraved. This material will transfer the design soaked in inks directly onto the paper.
Think it’s too simple? Wait until you see it in action!
“350 meters per minute! And our team members are stationed at the control table to ensure that all parameters are properly followed.“
The parameters to be controlled are the printing information desired by the customer:
“Of course, we don’t just limit ourselves to checking the final result but every single step. For example, on every production run, we check the pigmentation to ensure color accuracy, or the quality of the paper. These steps ensure that we are certain of the final product’s quality, and that’s essential for both us and the customers.“
Once deposited, the fresh ink needs to be dried. That’s why, once “stamped,” the paper follows its path upwards to pass through a heated band (up to 90 degrees). Once dry, it passes to the other side of the machine, now rolled into an imprinted reel.
The numerous advantages of flexographic printing
In the packaging industry, flexography immediately gained enthusiasts thanks to its speed, of course, but also due to its high degree of precision.
Compared to traditional printing, flexography allows for “long-lasting” printing, which is more cost-effective and, most importantly, higher in quality. Today, advancements in this technology have allowed for even further control by using cameras to inspect each printed unit. This is ideal for ensuring the absence of blurring or smudging on the final product.
Furthermore, flexography is an environmentally friendly method as it uses water-based inks and the plates used for printing are recyclable. This is an ideal combination with paper as a more sustainable raw material.
Modern flexography: the solution for your packaging!
Reliable, fast, and highly precise, this printing technique is ideal for achieving the best results on all your paper packaging.
If Semoulin Packaging is so concerned about working with the latest technological advancements, it’s because since its inception, the company has made it a point of honor to carry out the most meticulous work for its clients.
“Each product is prepared with the care that we would want to find if we were customers.“
Would you like to collaborate with Semoulin Packaging for your paper packaging? Contact us, and let’s work together on your new eco-friendly packaging